THE ORIGINAL CONCEPT
The first work carried out on the subject in my Laboratory at the University of Toulouse in the late eighties was entrusted to me by the company ORGANOCELL which had, from the work of KLEINERT, built a first demonstration plant in Pasing near Munich. The alcohols used as solvents and the reaction temperature of the order of 140 ° C apparently reduced the degradation of lignin but not the dehydration of hemicelluloses in furfural with finally a pulp of quality far from the expectations of the company that does not succeed the scaling up
These early works, however, encouraged me to continue and carefully consider acetic and formic acids, as destructuring agents, simply to avoid working under pressure with the prime objective at the time: the production of marketable bleached chemical pulp.
The state of the art of the moment mentioned hard conditions for formic acid, above 120 °C, with a production of furfural from hemicelluloses which disturbed me quite a lot and a necessary addition of sulfuric acid in the acetic acid which resulted in the same effects and consequences. Moreover, the mixture of the two was proscribed for reasons that were poorly explained.
The first tests showed that formic acid alone had a fairly good behavior at a temperature below 120 ° C but it was finally the mixture of the two which took the bet and was at the origin of this first technology because it was the first experimental protocol that had the ability to meet the criteria imposed for direct competitiveness with the oil refinery. The first patent filed directly by me in 1997 was going to be the base of construction of the CIMV company (www.cimv.fr)
THE CIMV COMPANY AND THE DEVELOPMENT OF TECHNOLOGY
The company was created in 1998 at my initiative with 4 partners including Thiéry SCHOLASTIQUE who was and is to this day its only President. The capital and therefore the relative position of shareholders varied over time.
The most significant movements were the entries of Robert LOUIS – DREYFUS in 2007 and the financial group PIERSON CAPITAL in 2012 for a cumulative private investment of around 50 million euros. The other significant financings came from European R & D contracts and research tax credit for nearly 30 million euros. The process is therefore summarized in the diagram below:
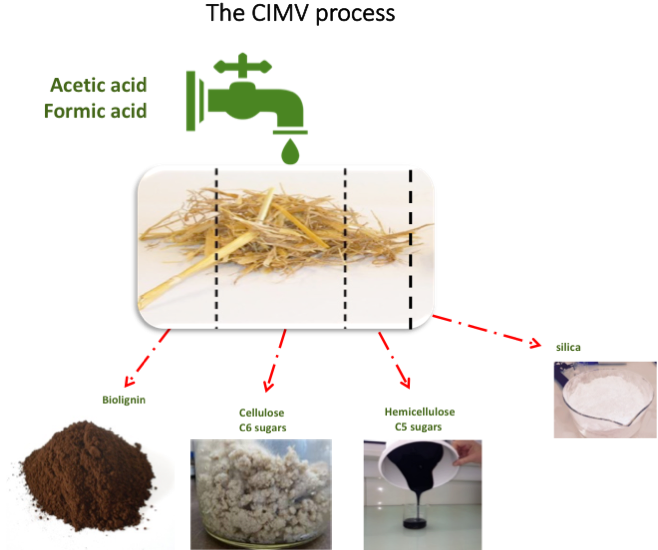
The raw material is heated around 105 °C with a mixture of acetic acid / formic acid / water. The solid phase, consisting of cellulose and silica if any, is separated from the hydro-organic phase by filtration / pressing.
The solid phase is freed of the excess of organic acids and treated with a basic solution which will dissolve the silica which will then be recovered by simple precipitation.
Depending on whether the cellulose pulp is intended for the production of glucose and / or ethanol or the production of paper pulp for printing / writing, the treatments it will follow will be quite typical of these processes.
The liquid phase is concentrated. Acetic and formic acids are recycled. Bioligninäis separated from the C5 sugar syrup by precipitation with water.
A first industrial pilot with a capacity of 1.5 T / Day of raw material was built in 2007 at the Pomacle sugar factory near Reims. It has made it possible to collect all the data necessary for the industrial scale-up and provides for 8 years the necessary samples of cellulose / glucose; C5 / xylose sugar syrup, Bioligninäand Biosilicaäfor smooth running, including 7 major European contracts, and CIMV’s industrial partners :
* The pilot unit of Pomacle / Reims 2007 – 2016
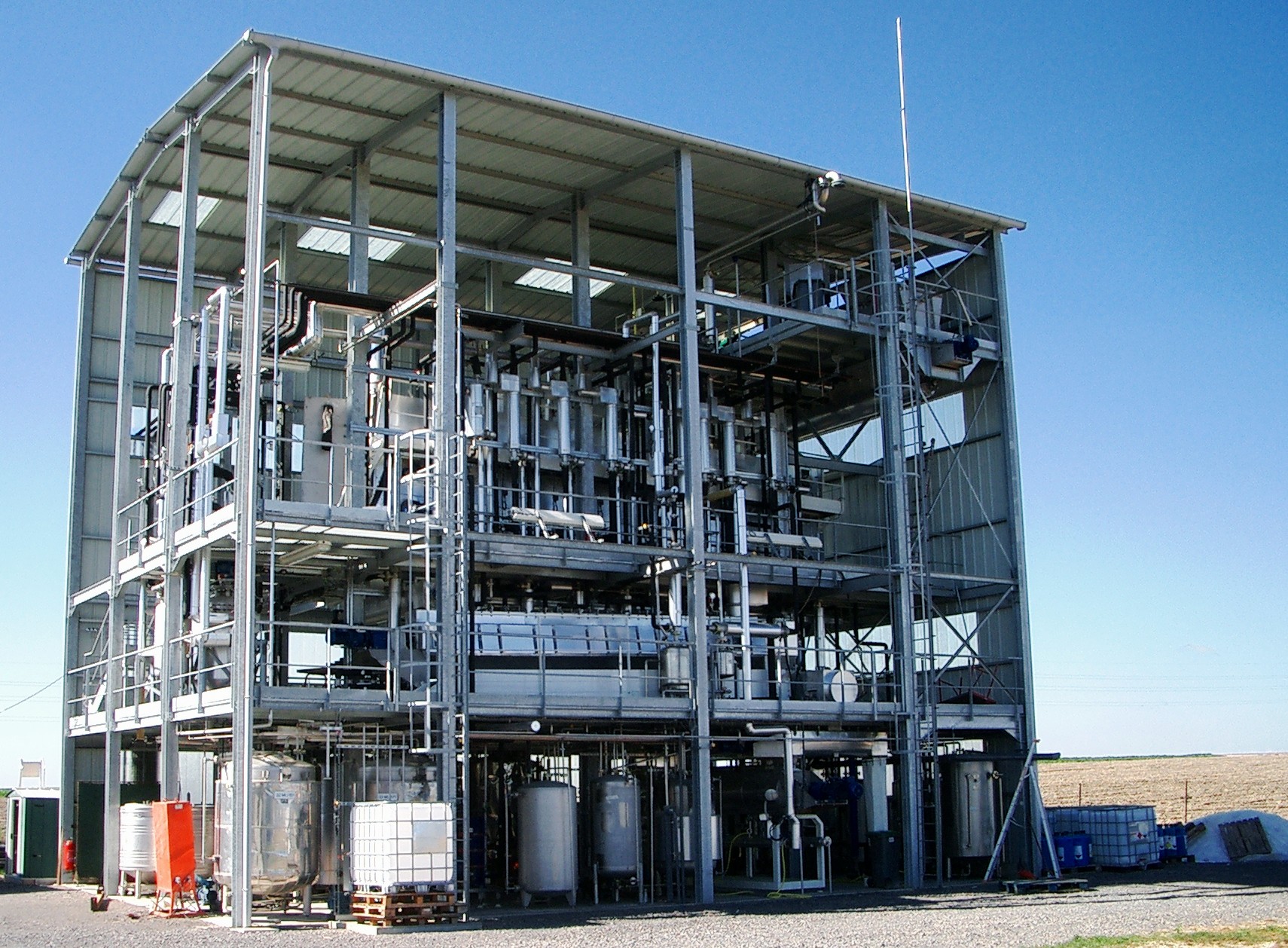
* The pilot unit of Compiègne / Paris CDG succeeded the pilot of Pomacle in 2016 and is now in operations to assist the transition to industrial production :
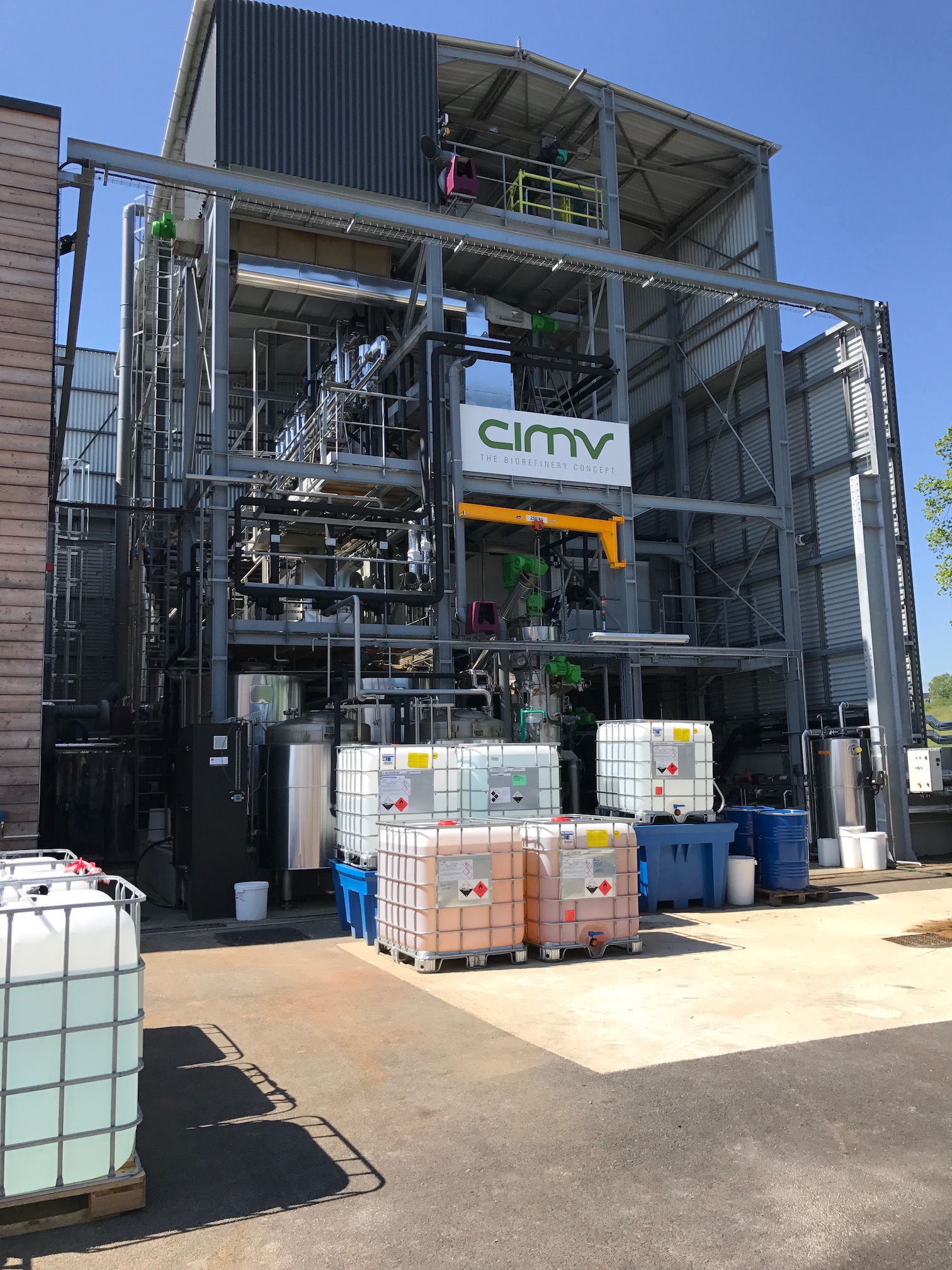
Patents and publications that protect and describe in detail the process and products are referenced bibliographic appendix and very easily accessible.
EUROPEAN R&D PROGRAMS
They referenced in the table below, using their websites, the final reports summarized in free access. From 2010 to the present, they brought together around 4 CIMV products more than 50 leading European companies, research centers and universities, establishing the industrial feasibility of both the process and the commercial development of the 4 CIMV products: cellulose, hemicelluloses, Biolignin and Biosilica.

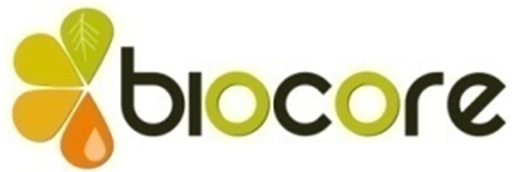
The European BIOCORE project, conceived and coordinated by Dr Michael O’DONOHUE, Director of the Characterization and Development of Agricultural Products Division (CEPIA), brought together around CIMV technology and its products, 23 Universities, European research and leading companies.
They analyzed in their area of expertise the industrial feasibility of the biorefinery concept that I developed with CIMV allowing the conversion of cereal by-products (straws, etc.), forest residues and short-rotation woody crops in a wide range. range of products including 2nd generation biofuels, polymers and materials.
Through the development of a range of polymer building blocks, BIOCORE has shown how at least 70% of today’s polymers can be derived directly from biomass.
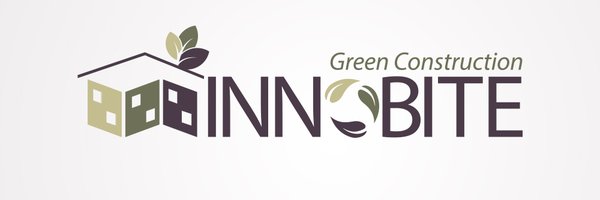
The European project INNOBITE (Innovative Biocomposites) aimed to convert agricultural waste into high performance products for the construction sector. These materials were therefore developed as part of an FP7 collaborative project of the European Commission. It was coordinated by the Spanish company TECNALIA and mobilized 10 Universities, Research Centers and leading European companies that worked from the Biosilicaäwhich is the essential part of the inorganic fraction of wheat straw and the production of nanocellulose from the cellulosic fraction produced by CIMV. These two compounds will be high performance additives in new polymeric composites.
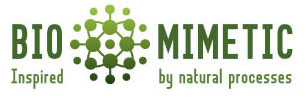
The BIO-MIMETIC project, coordinated by the PROCTER & GAMBLE Europe Company, established and patented in the wide world of household products the major interest of Biolignin™.
From different biomass sources, different homogeneous and constant batches of Bioligninähave been transformed into new bio-polymers through environmentally friendly enzymatic processes developed in the project and involving the enzymes laccases, tyrosinases, lipoxygenases.
Using the new bio-polymers, various household products and beauty treatments were obtained in the project including: a dishwasher, a compact cleaner for hard surfaces, a cream for the skin, a mask for the skin etc …
A life cycle analysis explored the environmental sustainability of the production of new biopolymers and their use in many of the new consumer products obtained.
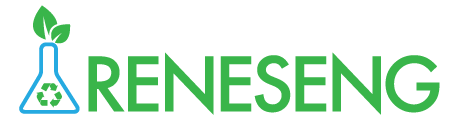
It is a European-wide training program that funds graduate European students, preparing their PhDs on research topics related to sustainable development.
In this way Aikaterina MOUNTRAKI has prepared in collaboration with the National Technical University of Athens her doctoral thesis on the modeling of the CIMV process under ASPEN and studied the possible symbiosis between the current processes of production of 1G bioethanol from cereals or sugar and the CIMV process which enhances the lignocellulosic support. The defense took place in Athens on March 27th2019.

The project is coordinated by the University of Aberystwith and mobilizes around fifteen European industrialists and universities. A first and major objective of the program is the production of succinic acid from fermentable sugars derived from cellulose (C6 sugars).
This intermediate molecule is a precursor of many finished products. The partners will rely on Biosuccinium™ technology, developed by one of the project’s industrialists. A techno-economic study and the evaluation of the life cycle will be carried out. This will include assessing the reduction of greenhouse gas emissions by this technology.
The second axis concerns the valorization of hemicelluloses (C5 sugars). New multifunctional enzymes will be developed to simplify the biorefining of these molecules. Biotechnological tools will be tested and developed to produce a natural sweetener: xylitol, and then bring its production to a commercially appropriate scale.
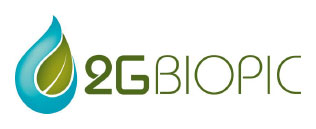
The aim was to build, on the basis of the CIMV technology, a pre-industrial demonstration unit capable of producing Bioethanol 2G from cellulose and hemicellulose from the CIMV process as part of the call for Biofuels H2020.
The extracted Biolignin™ must allow, by its very high level of recovery, an autonomous and profitable production of bioethanol for biofuel purposes, without subsidy of any kind, which would be a world first.
CIMV gathered around this program 7 European Societies and Research Centers to validate at the pre-industrial scale the remarkable results obtained by the BIOCORE program previously mentioned. It ensures more, given its level of commitment, coordination. The first step in the engineering study of the plant was completed. The construction phase that was to follow required a significant investment of CIMV. It was suspended pending the outcome of the talks entered into by CIMV with various large petrochemical companies that intend to acquire it to develop the technology.

The CARBOSURF project aims to develop new biobased processes and products and to solve bottlenecks in the fermentation production of bio-based biosurfactants and specialty carbohydrates. Specifically, it targets different glycolipid biosurfactants with a wide range of application domains including complex human milk oligosaccharides which find applications as nutraceutical, pharmaceutical and cosmetic ingredients.
The basic raw materials are 2G glucose and 2G Xylose, of lignocellulosic origin, resulting from the CIMV process. The project is coordinated by Prof. SOETAERT of the University of Ghent (Belgium).
The details of these programs, and their results when they are completed, can be found on their respective websites listed in the previous table.
COMMERCIAL PRODUCTS
Cellulose et Bioethanol 2G
Cellulose extracted by CIMV technology has the classic characteristics of a commercial chemical pulp currently on the market. Its technical characteristics have been established with the Technical Paper Center of Grenoble and the company ARJO – WIGGINS.
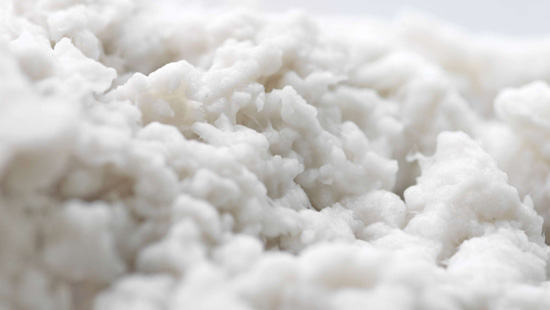
This type of valorization of cellulose in my biorefinery concept, although of major interest for producers, came at a time when the paper went through a major crisis at the beginning of this century.
The financial crisis of 2008 being added, this situation did not encourage the big global paper groups to invest in totally new factories, of an exceptional profitability thanks to the BioligninTM, yet adorned with all the environmental virtues required by the sustainable development.
The growing demand for second-generation (2G) bioethanol took the lead. Cellulosic fibers obtained from lignocellulosic residues are also formidable sources of Glucose for more than 90% and Xylose for the remaining part, of a rare efficiency for the production of 2G bioethanol.
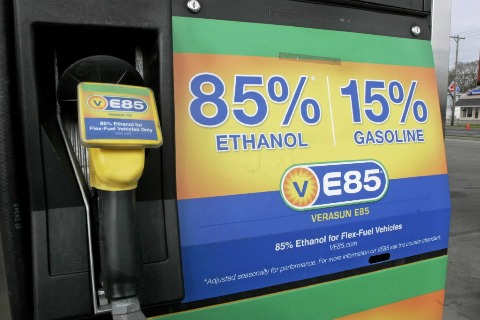
The prior separation of the BioligninTM greatly facilitates the hydrolysis of cellulose and hemicellulose oligomers. The absence of fermentation inhibitors such as furfural and wood residues present in all competing processes and the mobilization of all sugars makes it possible to post exceptional production rates of Bioethanol 2G which can reach 370 – 380 L per ton. of lignocellulosic material when the competition peaks at 280 L.
The sugar environments thus obtained, which are free of lignin, are of the same major interest for all fermentative productions of synthetic biology because of their particularly competitive purity, concentration and price. The yields obtained by industrial partners for the production of lactic, succinic or itaconic acids confirm the statement.
C5 Sugars
When Xylose 2G, which is the main component, is not mobilized by Bioethanol production, a large number of industrial valuations exist.
The first, very simple but profitable, is the direct use of this concentrated sweet juice, obtained after precipitation and separation of BioligninTM as animal feed due to multi-functional properties.
Xylose has the capacity, like the currently used formaldehyde, to react reversibly with the amino termini of vegetable proteins of cattle and to regulate their digestion on the one hand, and on the other hand to bring an energy supply to the molasses currently used, resulting in increased production of meat and milk. In addition, a small residual amount of formic acid will assist in bacterial control.
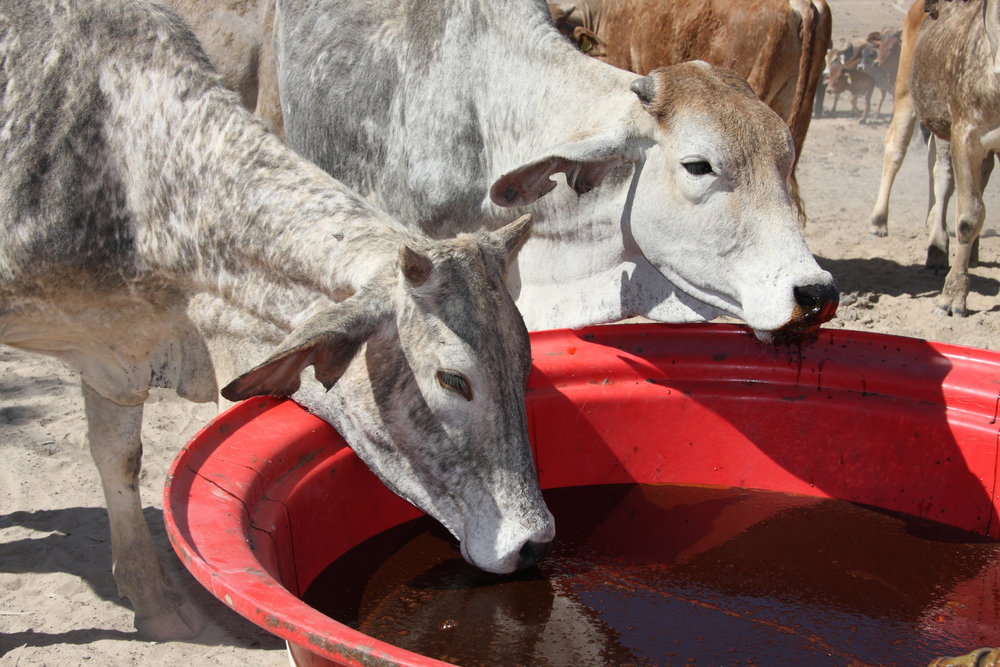
Its second immediate application is the production of Xylitol, which is of particular interest to the DOW – DUPONT DE NEMOURS group, which has a virtual monopoly on the production of this remarkable sweet sweetener.
This sweet juice can also relaunch in excellent ecological and economic conditions the production of furfural which collapsed today to a few tens of thousands of tons when it exceeded the million at the end of the last century. This is the route of access to furfuryl alcohol, its resins with exceptional resistance to fire and its many derivatives.
Biolignin™
BioligninTM is therefore a natural phenolic oligomer whose hydroxymethyl functions have been partially acetylated and formylated. This structural peculiarity gives it a particularly interesting reactivity which classifies it as a reactive macromolecule where all the lignins present on the markets to date are considered only as filer in the polymer materials likely to integrate them.
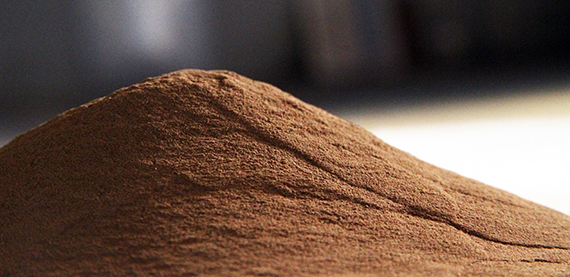
The commercial value of BioligninTM is very easy to evaluate since it can replace weight to weight phenol and its derivatives, without significantly changing its conditions of industrial implementation, in most of their applications.
Petrochemical production of phenol is currently around 8 million tons worldwide, with consumption of by-products increasing by 4 to 5% per year. Since it is no longer possible to build new phenol production units around the world, especially in view of its dangerous nature, the major world producers of phenol, with whom I have traded, see the lignin arrive with kindness because coming first in green complement of their product.
The price of phenol has, in recent years, varied between 1200 and 1700 € / T, depending on oil prices. It will therefore be the price of Bioligninäwhich becomes the decisive economic advantage of technology.
Thus Biolignin can, among other things, replace qualitatively and quantitatively :
- Phenol in phenolic resole or novolak resins at substitution levels of 50 to 70%
- Bisphenol A in epoxy resins, depending on the application, from 10 to 80%
- Polyethylene glycol (PEG) in foam polyurethanes and films in particular,
- Carbon black in whole or in part in elastomers
Biosilica™
It is one of the major constituents of rice straw, itself the raw material of choice for my technologies. It should be known indeed, as stated previously but it will never be said enough in these times of energy transition, that the rice straw is systematically burned on fields precisely because of its silica level which is close to or exceeds 10% by weight. which makes it perfectly indigestible for animals and slows down its decomposition in the soil to the point of disturbing the next crop.
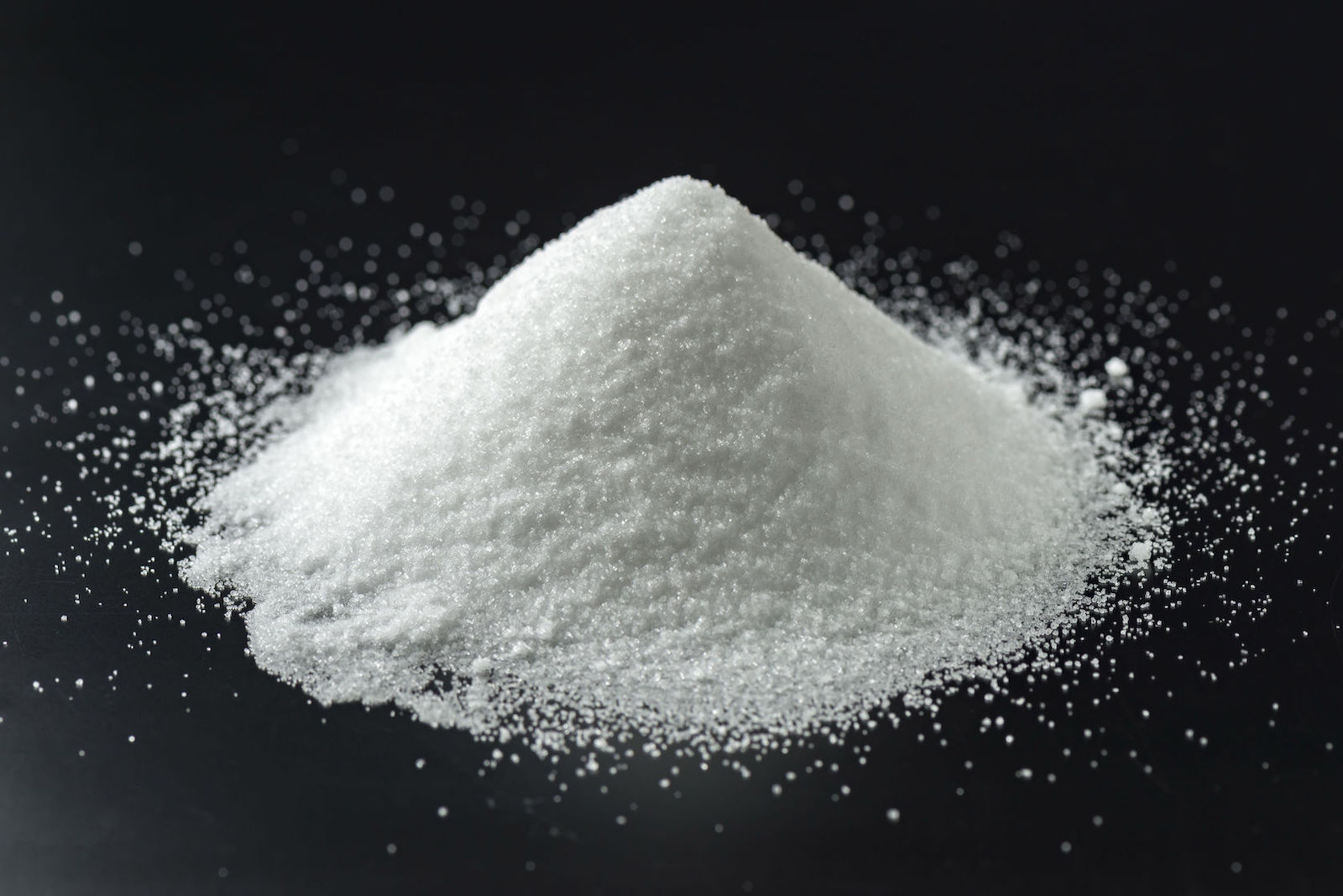
That’s nearly a billion tons of lignocellulosic residues that go up in smoke each year, without any benefit to anyone when they could easily substitute not far from the same amount of oil according to my previous remarks, namely 1/5 of world annual consumption!!!
The BiosilicaTM is obtained very easily after the basic washing of the cellulose fibers which dissolves the silica deposited during the growth of the rice on said fibers. It is then sufficient to neutralize the aqueous solution obtained to recover the precipitated silica.
It is to date the only precipitated silica of plant origin whose production cost is most limited especially in terms of energy which is a decisive commercial advantage today compared to its current industrial counterpart.
The markets of BiosilicaTM, registered trademark of CIMV as well as BioligninTM, are diverse, varied and remunerative. We find it as:
- reinforcing agent in polymers, especially in elastomers, more particularly in tires or it partly replaces carbon black
- abrasive agent in different industrial sectors,
- additive for paints, coatings, etc.
The world market in 2015 was 2.2 MM € for a production exceeding one million tons.
INDUSTRIAL DEVELOPMENT
It will pass, as a result of ongoing negotiations with different oil groups by the takeover of CIMV by one of them.
Currently the CIMV process is the only existing process in the world with the industrial and commercial potential required to produce bioethanol 2G with Bioligninäand Biosiliceä, without any kind of subsidy, at the world price of bioethanol 2G, under the required conditions. previously summarized for the CIMV plant refinery to be in perfect competition with crude oil refineries at $ 40 / barrel.
I ceased my activity of Inventor / Creator / Consultant with the company CIMV end of June 2016 at the request of the group PIERSON CAPITAL who, wishing to take full control of CIMV, therefore offered to buy my shares.
A satisfactory agreement between the two parties put an end to my contractual functions with CIMV on 28/06/2016, with immediate effect, after 18 years of loyal service.
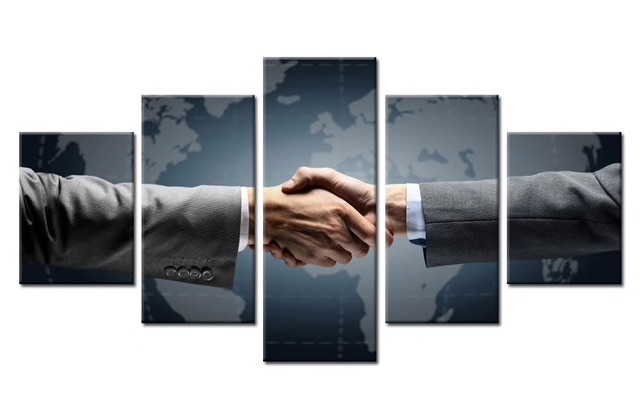